In the fast-paced and dynamic world of food production, maintaining a high standard of cleanliness is essential to ensure food safety and prevent contamination. One crucial aspect of this process is the regular and efficient washing and sanitisation of tote bins or buggies. These containers play a vital role in storing, transporting and handling various ingredients and products around the site or between processes. Properly cleaning and sanitising them, not only ensures robust hygiene standards, but also safeguards product quality, prevents cross contamination, and protects consumers. In this Tech Talk we will explore the importance of tote bin (or buggy) washing and investigate the effectiveness of various jetting systems used within the industry.
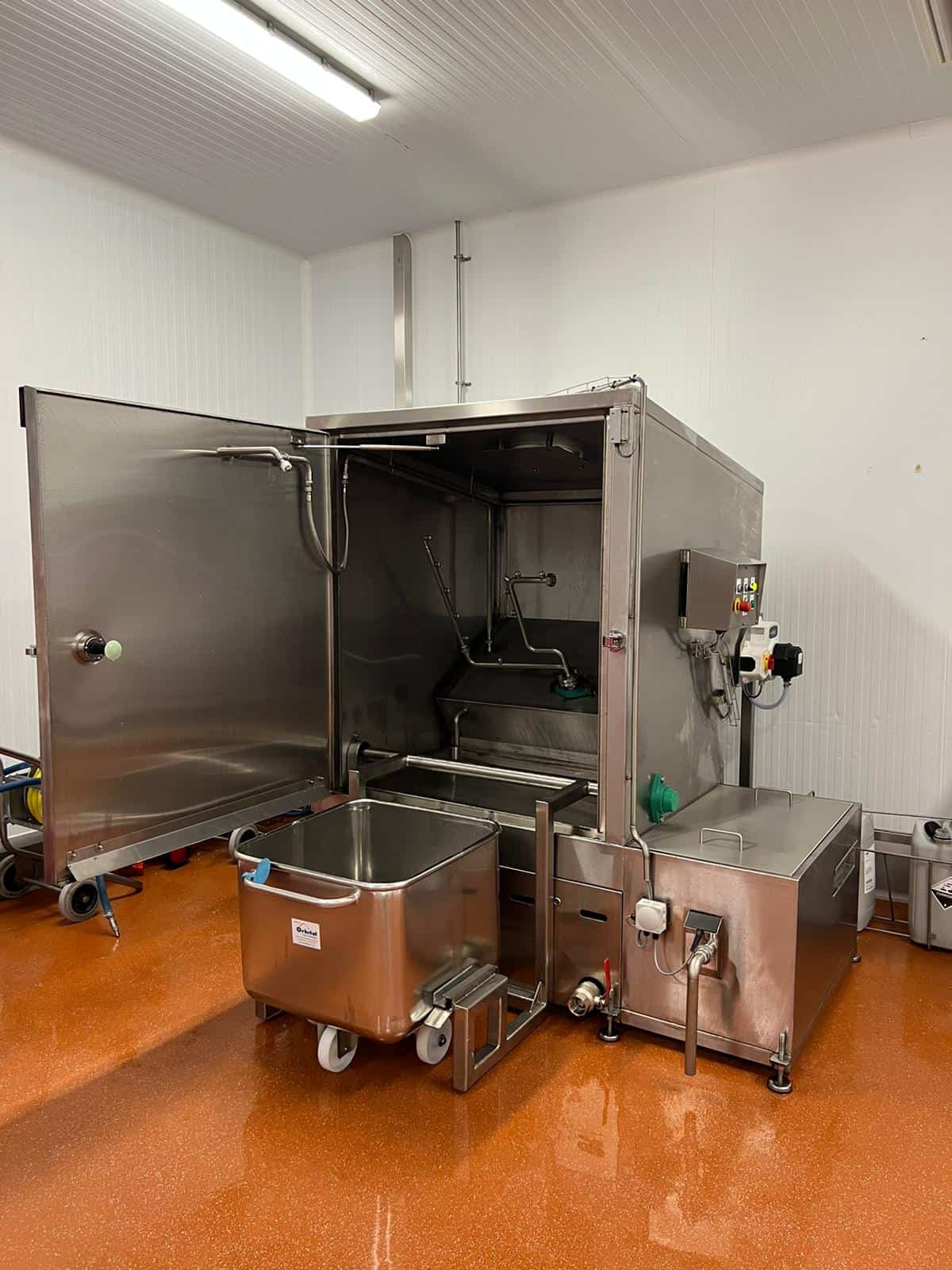
Safety and Compliance
Food safety is a primary concern for food manufacturers and consumers alike. Tote bins, which come into direct contact with raw materials and intermediate products and finished goods, can harbour harmful bacteria, allergens, pathogens and foreign contaminants. Regular cleaning routines reduce the risk of cross contamination and maintains a hygienic environment within the food processing facility.
Food producers and processers are subject to strict regulations and standards set by governments and industry bodies, and proper cleaning of tote bins and buggies are necessary to meet these requirements.
Risks
Moisture, warmth and organic residues provide an ideal breeding ground for microbiological growth, and tote bins that are not thoroughly cleaned can become a potential source of bacteria, moulds and pathogens, and can also allow the transference of soiling between areas, especially on the wheels.
It is also important to thoroughly wash bins in order to prevent allergen transfer between products, ensuring consumer safety and approved manufacturing processes.
Efficient Washing Methods
There are several different methods of cleaning tote bins/buggies, within a food factory. The basic method is with use of a high-pressure lance, where the inner and outer surfaces are jetted manually. This can have a detrimental effect on the floor of the washroom and the bin itself if the bins are tipped over, unless a tote bin wash frame is employed. Even then, thousands of litres of fresh water per day are used and when this commodity is expensive, with the factory paying for both fresh water and effluent charges, it can be an inefficient way of cleaning, not to mention the environmental impact. High pressure washing in this manner can also lead to cross contamination due to airborne aerosols, meaning that controlled segregation of the wash area is required.
In addition to the above issues with manual cleaning, the facility is relying on cleaning staff to determine what constitutes a “clean“ bin, and to follow required standards consistently.
This is where the use of a tote bin washer can quickly pay for itself in a short period of time, minimising utility usages, introducing a consistent level of cleanliness and speeding up the washing process.
Various wash cycles can be incorporated to cope with the most contaminated bins, from pre-washing, through to hot water final rinse, and depending on the type of machine employed, different rates of throughput.
Even when the decision is made to purchase a machine, it is important to investigate the different wash methods employed by different manufacturers.
Below, some of the general cycles employed within a cubicle system, are outlined.
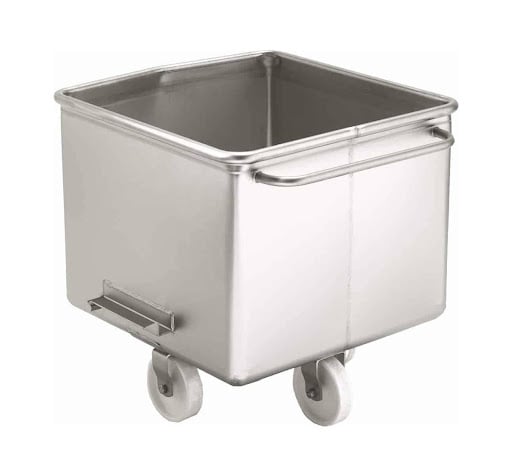
Pre-Wash
If the tote bin is heavily soiled or has large amounts of sauces (mayonnaise etc), then it may be advisable to look at a pre-wash cycle on the machine. These can be hot or cold, depending on the type of soiling. If the soiling is liquid or sauce, it is recommended that the pre-wash water should be directed straight to drain, which will avoid contamination of the main wash water and prevent the detergent solution becoming saturated and less effective. In this case it is important to select a machine that uses the minimum amount of water and energy to do this.
Detergent Wash
A detergent wash cycle, generally at 65°c/185°f, is used to jet the soils from the bin, and is re-circulated and filtered to remove debris from the solution, ensuring the detergent within the wash section maintains its effectiveness. Various methods of filtration can be employed, including screen filters, filter drawers, or in the case of heavy solid soiling, automatic belt or rotary screen filters.
Final Rinse
A final rinse of fresh water is used to remove detergent residues from the bins prior to exiting the machine. This water can either be heated or fresh ambient from mains, depending on technical requirements, and can be re-circulated (on heated option) to minimise water usage. Heating the rinse can assist in “flash drying of the bin on exit from the machine.
A secondary final sanitising/disinfecting cycle can be incorporated following the final rinse if this is a specific requirement of the technical department.
Whichever combination of the above processes are employed, it is important that the washing is carried out as efficiently and effectively as possible, minimising the amount of water and energy used.
Although the above cycles can be available on many machines, there can be a difference in how each manufacturer approaches the jetting and cleaning of the bin. The differing methods found within machines are explained and investigated below:
-
Internal Spray Ball / Jetting Array
This method relies on the water pressure from the pump to provide the energy to rotate the ball or jetting manifold within the bin/buggy in order to remove the debris from the internals. This method can be effective, as the water droplet size is generally greater than a fan spray jet, giving an improved impact over a longer distance but sometimes this method can take time for the spray to reach all parts of the surfaces, thus increasing the wash time, and may not be as effective on products such as cut vegetables, which can adhere to the bin internals. Also pump flow rates will be higher given the amount of water needed to produce the required internal coverage and to provide the outer jets with sufficient flow to clean, this may increase the motor size of the pump required.
The internal ball or rotating faces within the head can be susceptible to debris build up, and can lead to jet failure unless fine filtration is employed, as free rotation of the head is crucial to the wash operation and can be affected by the soiling within the system. This can result in excessive maintenance down time, or more frequent cleaning of tanks etc.
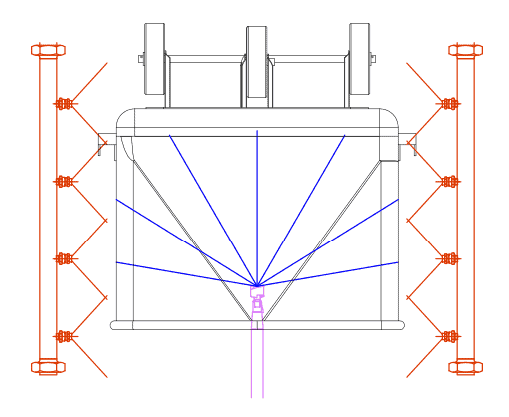
- Conventional Fan Jets
Jetting with conventional fan jets coupled with either fixed or oscillating spray bars, can be an effective way of jetting but can also have its limitations. The external jets can be located quite close to the bin surfaces, but the internal jets must reach the bin base from at least 750mm (30”) away, which can result in reduced impact due to atomisation. However narrow angled jets can minimise this atomisation, but increases the flow required for coverage. Also the front and rear internal faces can have reduced jet contact time with flat fan sprays unless cone pattern sprays are used.
Quick release nozzles can minimise any clean down times, but care must be taken with plastic bodied jets as they can become misaligned when removing the tips for cleaning, so stainless steel quick release jets should be used, in order to prevent this.
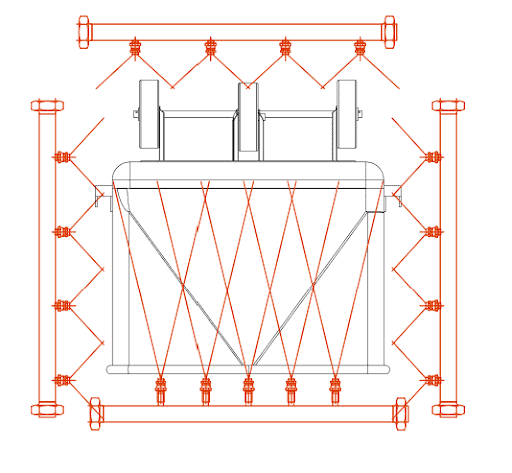
- Motorised Jetting Arm
Employing a rotary motorised manifold can both reduce the number of jets required for cleaning, reduce the energy required for pumping, and minimise the process time of the wash cycle.
The bin is inverted over a rotary arm, similar to the rotary ball type process, fitted with flat fan jets, that rotates inside the bin, whilst jets clean the external surfaces and wheels simultaneously. This allow the jets to be located closer to the bin/buggy surfaces than either of the above options, with the flat fan providing a pressured “wiping action” on the soiled areas. With the clever use of valves, the same pipework and head can be used for both wash and rinse cycles, which can assist in flushing the wash pipework, and if a pumped heated rinse is employed, the same pump can be used, making the unit more compact. This method can provide a more efficient wash process, minimising both cycle times and utility usages, making the purchase of the machine more attractive to the business.

As shown above there can be many solutions offered to achieve the same goal, and various manufacturers will have their own justifications for the methods used within their system. As long as the unit provides the client with the desired result, there is no right or wrong in any of the above systems, but there can be a difference in utility usages and process speeds.
At Unitech Washing Systems, the motorised jetting arm system is employed on our tote bin and bulk bin washers. This allows us to provide minimised cycle times and lower utility costs whilst providing, what we believe, is a superior and consistent wash quality. Using stainless steel jets, the jetting efficiency is maximised, and clean down times are reduced by using quick release nozzles, hygienic pipework and manifold flushing points.
In addition to the cubicle system investigated above, we also offer in-line systems for higher speed applications, but can incorporate the same features (pre-wash/wash/ rinse) as the cubicle systems.
For more information on tote bin washing or our extensive range of wash equipment, please visit the products page on our website.