Probably the most important feature of a washing system is the jetting itself. If you cannot effectively cover all areas of the product to be washed, then the efficiency of the system is compromised from the start. There are many systems on the market that are supplied ‘off the shelf’ or have a standard jetting pattern that the manufacturers supply for a particular range of machine.
That is acceptable if you are looking for a general wash, but not if you are looking for an efficient clean.
Types of Jetting
If you take your domestic dishwasher for instance, the jetting is very general and relies on the ricochet effect to ensure surfaces are covered and cleaned. However this can take up to 2 hours to produce a result. In a food production facility you do not have this luxury, so the position of the jetting needs to be more targeted to reduce the time required to clean the products.
Mechanical action (jetting) and time are 2 of the 4 factors required for efficient cleaning. If we reduce the time required, then the mechanical action needs to increase/improve, and this is where good jetting design is paramount.
In a machine, either the product moves or the jets move in order to create the ‘wiping’ action required to remove the debris. If the angle of incidence is too shallow or too great, then the effect you will get is varied, so if the jetting angles can be adjusted within the manifold design, then the optimum angles can be achieved.
Pump pressure and water velocity are also factors to be considered. Generally with normal flat fan or cone jets, the further away from the product, the less effect the jet has due to the atomisation of the water away from the tip. Atomisation reduces the cleaning effect and can also increase the heating costs due to heat loss by the atomised water. A lower pressure will reduce the atomisation effect, but will not necessarily provide enough pressure to wash. A higher pressure may increase the atomisation effect and reduce the optimum distance, so each system needs to be designed to exploit this. This can be easily demonstrated when using a high pressure hose to clean your car/patio. If you move the nozzle further away from the surface, the more atomisation you experience and less cleaning action, so there is an optimum distance for the most effective result.
This refers back to the previously discussed ‘Dustbin and Teacup” syndrome‘, where large and small objects are washed in the same machine. The jetting (unless specific or adjustable between products), can rarely suits both items.
Optimum Jetting Designs
At Unitech Washing Systems, each product is evaluated, and the jetting systems (and arrangements within the machines) are plotted on a computer and adapted to suit, giving an optimum cleaning efficiency.
Angle Too Shallow – Correct Angle – Angle Too Great
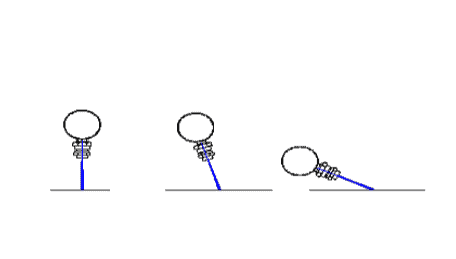
<—- Product Flow
In order to increase jetting efficiency further, consideration also has to be given to the delivery pipework. Smooth bore manifolds, with hygienic fittings (RJT or IDF fittings) offer continuous flow without obstructions within the bore, which can minimise silt and debris build up. Box section pipework, which can be found in some competitors’ machines, introduces flow disruption and sudden changes in direction. This can reduce the performance in the system, and is often difficult to clean thoroughly.
Flushing points located at the end of a pipe run should also be considered as a way of quickly cleaning the inside of the manifold pipework, without having to strip down the whole of the system, thus saving time and maintenance costs.
As you can see from the above image, efficient jetting is not just a matter of throwing water onto a product – it is a little more involved. If designed correctly, you can maximise performance, improve machine cleanability, and minimise cost.